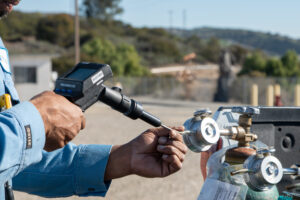
What Are the Limitations of Method 21?
April 22, 2023
Throughout the 1970s and 80s, leak detection and repair requirements made their way into various regulations across multiple industrial segments. Method 21 became the standard practice for complying with many of these regulations.
When conducting a standard Method 21 inspection, a technician uses a handheld detector to manually scan the surfaces of regulated components in industrial facilities to find fugitive emission leaks. For example, a technician may hold the detector around a valve and its connectors to look for a concentration reading. If the concentration gets above a certain threshold—let’s say 500 parts per million (ppm)—that would imply there’s a leak.
The idea of scanning for a leak using a Method 21 instrument sounds simple enough, but Method 21 has more than its fair share of technological limitations and costly setbacks.
Here are some of the most consequential Method 21 limitations:
Probe position
For starters, a technician must scan each component in its entirety one at a time. As you can imagine, that can be a time- and labor-intensive endeavor. But there’s more to it than resource management. To detect a leak using a Method 21 device, a technician’s device must be positioned directly on top of the leak.
And if that technician is off by as little as one centimeter, they have up to a 57% chance of missing the leak. This is according to an EPA study. The technician must also scan slowly enough to allow the device to get a proper reading. Move too quickly, and the technician can sweep right by a leak without detecting it.
Efficiency
Method 21 can scan approximately 30 to 50 components per hour, or around 240to 400 components per day. Most components don’t leak, which means a vast amount of time is wasted in monitoring non-leaking components.
Accessibility
Method 21 can’t monitor insulated components or components that are elevated or otherwise difficult to monitor. For components suspended two meters or higher, technicians are often forced to use ladders, scaffolding, or hydraulic lifts to reach them. This adds time and introduces additional safety hazards.
Reduced frequency
Due to its many limitations, regulations requiring Method 21 often allow for reduced monitoring frequencies for certain types of components. The impact here is that if one of those components does happen to leak, it could be months, if not years, before that leak is found.
What are ghost leaks?
One of the major drawbacks of Method 21 is the creation of “ghost leaks.” Ghost leaks occur when a technician detects gas around one component that’s originating from somewhere else. This increases the likelihood that a technician identifies the wrong component as the source of a leak. Conversely, with an Optical Gas Imaging (OGI) camera used in AWP, a technician can visually pinpoint the exact source of a leak.
A real-life case Study of ghost leaks
Here’s an example of a ghost leak from an actual Method 21 survey. A Method 21 contractor identified a leak stemming from the valves on a tank’s liquid level gauge. A follow-up OGI inspection was conducted, which revealed that the leak originated from the tank’s level gauge faceplate located underneath the valves.
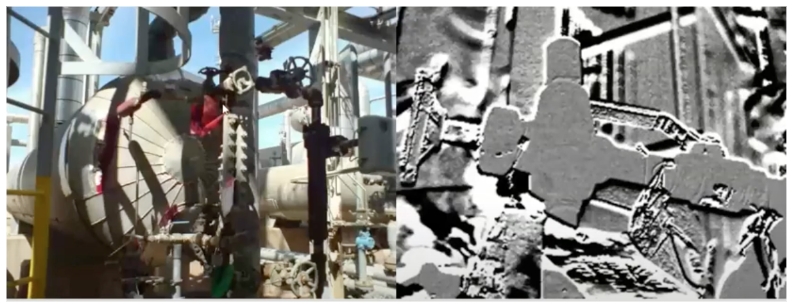
**Use GIF animation beginning at 14:30 of webinar video**
The faceplate where the leak originated wasn’t even a regulated component, meaning a Method 21 technician would never have scanned it as part of their survey. In comparison to Method 21 Devices, an OGI camera monitoring the regulated components of the liquid level gauge would have likely captured the face plate when framing up for the valves—and therefore would have detected the leak directly at its source.
Without the follow-up OGI survey, it’s likely that the face plate would have been needlessly replaced while the actual source of the leak remained unfixed.
Overcoming the drawbacks of Method 21
With AWP, LDAR programs can utilize the efficiencies of OGI technology to overcome the costly limitations of Method 21. Of course, conducting a truly beneficial OGI survey still requires a thoughtful approach. Learn the most common OGI pitfalls and how to avoid them.