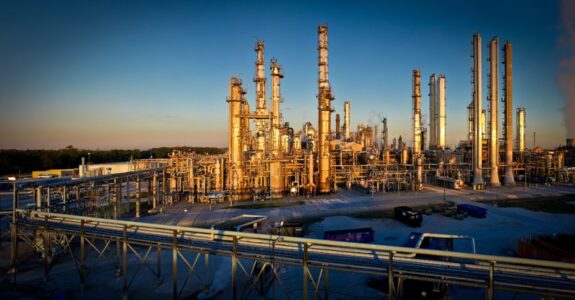
What is Alternative Work Practice?
April 18, 2023
By: Jared Metcalf
Alternative Work Practice (AWP) is a leak detection method used to scan for emissions leaks at industrial facilities. It allows leak detection and repair (LDAR) programs to incorporate Optical Gas Imaging (OGI) cameras to periodically check equipment for leaks using infrared imaging.
LDAR programs can use AWP in lieu of federal Method 21 monitoring requirements found in 40 CFR Subparts 60, 61, 63, and 65. AWP can also be used in place of the Method 21 monitoring requirements in many states. The EPA released its ruling on AWP in 2008.
What are the requirements of AWP?
AWP requires a full scan every other month of all assets using an OGI camera. Regulated components must be monitored at least once a year using standard Method 21 equipment. Additionally, OGI cameras must have the capacity to see the gas(es) in question within a specific level of detection sensitivity. OGI camera operators must also conduct performance tests on their cameras with a maximum viewing distance, and they must record each survey in its entirety.
Why use AWP?
At Montrose, we’ve seen the benefits of AWP in practice, with many clients increasing monitoring efficiencies while lowering program costs. On a federal level, the EPA has acknowledged that, “When used, the AWP provides equivalent control and appears to be less burdensome to implement,” (73 FR 78202).
Many state governments note the benefits of AWP as well. In Texas, regulators observed that “more frequent monitoring with the optical gas imaging instrument allows larger leaks to be detected and repaired faster than a leak might have been under the traditional LDAR work practice… optical gas imaging instruments is considered to be equivalent or superior to the traditional work practice using Method 21,” (35 TexReg 5294).
Benefits of OGI technology for LDAR
Efficiency and cost
OGI inspections are 20x faster and can be lower in cost compared to surveys done with standard Method 21 instruments.
Accuracy
With OGI, technicians can pinpoint the exact source of a leak. This level of accuracy eliminates the possibility of costly ghost leaks.
Accessibility and safety
OGI camera operators can safely scan components that were previously inaccessible or even unregulated. The ability of an OGI camera to scan hard-to-reach components from a distance reduces the need for scaffolding, hydraulic lifts, ladders, etc. As a result, survey times are reduced, and potential work hazards are avoided.
Simplified approach
AWP reduces LDAR program administration costs and is less burdensome to implement.
Emission reduction
Because OGI surveys are faster and more encompassing than Method 21 surveys, leaks of all sizes are more likely to be detected and repaired quicker.
What are the best practices of AWP?
Performance tests
A technician is required to conduct a performance test on the OGI camera before the start of each survey. But conditions can change as a survey progresses. Environmental factors such as temperature and humidity can impact OGI camera performance. An OGI camera can also perform differently between interior and exterior locations.
Technicians should conduct a performance test on their cameras anytime environmental and location variables shift to a significant degree. This is where a well-trained and experienced OGI technician is vital.
We also recommend that technicians use a rangefinder to ensure a proper maximum distance is maintained when they conduct a performance test.
Leak measurement
Aside from finding and estimating a leak using an OGI camera, each detected leak should be tested with a standard Method 21 device. If possible, we also recommend measuring each leak with a high-flow sampler.
Data recording
Trying to capture a survey in a single bulk recording can be risky. An OGI camera can malfunction during hours-long recording periods, which means you risk losing your footage. Additionally, large video files are cumbersome to manage. That’s why we recommend recording surveys in 30-minute increments, creating smaller half-hour video files. These video files should be backed up on-site.
When a leak is detected, we also recommend capturing it on video for 10 seconds and taking a picture. In the picture, the leak should be identified with a leak point ID.
Repair confirmation
Every leak found, regardless of the tool used, should be bubble tested. Most leaks will produce bubbles. By referring to the video and repeating the bubble test once the repair has been made, the technician responsible for fixing the leak can ensure that the leak has indeed been stopped.
There’s a lot more to AWP
We’ve barely scratched the surface of AWP and how it stacks up against Method 21. To gain a better understanding of AWP and its benefits, take a moment to learn about the major limitations of Method 21, including one of its most devastating challenges: Ghost leaks.
Jared Metcalf
SVP of Air Emissions Services
Jared Metcalf has over 20 years of Oil & Gas Industry experience. His extensive experience in providing professional fugitive emission monitoring services across North America and internationally has given him the expertise to help our clients meet their compliance/voluntary requirements. Jared specializes in the design, setup, and implementation of LDAR programs using Optical Gas Imaging.