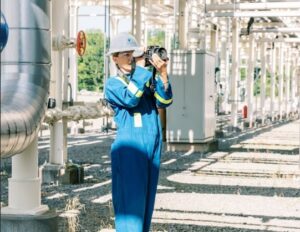
How to Get the Most from OGI Surveys
April 22, 2023
While surveys conducted with Optical Gas Imaging (OGI) cameras can make leak detection and repair (LDAR) programs highly efficient, they still require preparation, diligence, and thoughtfulness.
In other words, a good OGI camera alone does not equate to effective Alternative Work Practice (AWP). Like any method, AWP comes down to following proper steps to maximize leak detection while meeting compliance and minimizing costs.
Let’s walk through two of the most harmful OGI pitfalls that drain resources and negatively impact leak detection ability. We’ll also go over how your LDAR program can overcome these pitfalls to get the most from your OGI surveys.
LDAR Pitfall #1: Inexperienced technicians
Training and experience matter. In fact, insufficient training and inexperienced OGI camera operators have the biggest impact on survey results. In a 2020 study conducted by the Energy Institute at Colorado State University, experienced OGI surveyors found nearly twice the number of leaks than less experienced ones.
We’ve seen the difference that training and experience make firsthand. In one instance, one of our OGI technicians happened to be at a facility at the same time as a technician who was conducting a greenhouse gas survey. Both technicians were using the same model OGI camera. The other technician found 14 leaks. Our technician found over 120. Upon further inspection, it was revealed that the other technician had minimal experience. They had simply rented a camera and tried to conduct a survey.
An in-depth training and auditing program is vital to overcoming this pitfall. The OGI camera is an effective tool, but it needs to be in the hands of an experienced, capable operator. At Montrose, we invest a lot of time and focus in developing a training program that produces skilled and knowledgeable technicians.
Inexperienced OGI technicians generally… | Experienced OGI technicians always… |
Don’t record components from multiple angles. Leaks can hide against the background of an angle but be revealed against another. | Frame components from multiple angles to spot leaks against different backgrounds. |
Move the camera from scene to scene without taking the proper time to pause and view each frame and angle. They often scan too quickly and miss components/areas. | Maintain a high degree of quality control. They observe proper technical procedures and adhere to training requirements and individual and team performance audits. They understand the importance of taking time to review each and every scene. |
Are highly inefficient. They don’t understand which survey conditions require more time for an adequate scan and under which conditions they can move quicker. | Highly efficient. They ensure that all processes and equipment are scanned and continuously perform a qualitative analysis of the thermal properties of the background to maintain adequate thermal backgrounds. They know when conditions require more time for proper scanning and when they can move quickly from one task to the next. |
LDAR Pitfall #2: Poor data management
Data management is where most LDAR programs fall apart. When a leak is found, the surveyor must share the information with stakeholders, including the onsite personnel responsible for fixing the leak. The person tasked with the repair needs a way to retrieve the leak information and log all repair data before, during, and after the task is complete. On the backend, the LDAR program needs a way to access and compile all survey and repair data for compliance reporting.
Essentially, from survey to reporting, data is generated at every point—and trying to manage all of it in disparate systems can cause miscommunication, time-wasting missteps, and potential non-compliance. At Montrose, we’ve seen systems that are nothing more than literal binders full of handwritten notes. We’ve also seen multiple Microsoft Spreadsheet files spread over multiple computers, all with inaccurate or incomplete information.
To overcome this pitfall, we recommend a centralized LDAR database, where stakeholders can access, manage, and view all LDAR data in a single place.
An LDAR database should:
- Provide easy communication of your LDAR program to stakeholders
- Scheduling surveys
- New leak data and repair due dates
- Tracking program and facility performance
- House all survey/repair data
- Contain all LDAR data no matter the practice (Method 21 or AWP)
- Ensure that field data is accurate and complete
- Provide a way to track inspections and view progress
- Provide a way to enter repair activities and view progress
- Connect with a work order system via API
- Compile reports that are comprehensive and accurate
An example of efficient LDAR data management
Montrose technicians in the field collect leak data using the Target Track application on their mobile Android devices. The leak data can come from either AWP or Method 21 and is instantly synced up with Target Online.
Target Track mobile app for Android devices
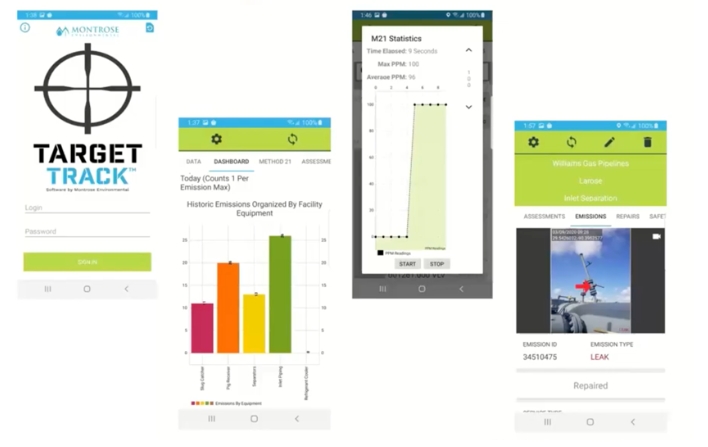
**Screenshot from 32:14 of webinar video**
Target Online serves as the interface where users can log in and review leak information. They can see where leaks are and evaluate the performance of their LDAR program at one or more facilities. For example, they can drill down to a specific site to see the number of leaks, how many are overdue for repair, the monetary value of those leaks, etc. Using the same system, users can also compile and report LDAR data for internal purposes or external compliance obligations.
Target Online dashboard
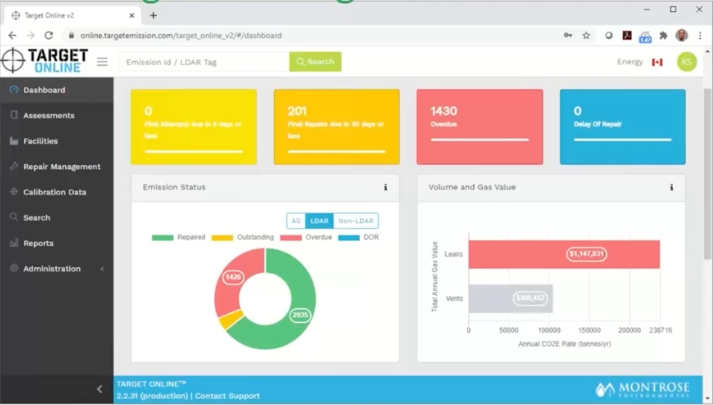
An LDAR database should remove the weak link between communication and data management. In the case of Target Online, it communicates with a work order system through an API. This way, it can automatically trigger the creation of a work order so a leak can be fixed, and it updates data automatically once the work order is closed out and the leak is repaired. All data is collected and organized, ready for analyzing and reporting.
How Target Online communicates with work order systems
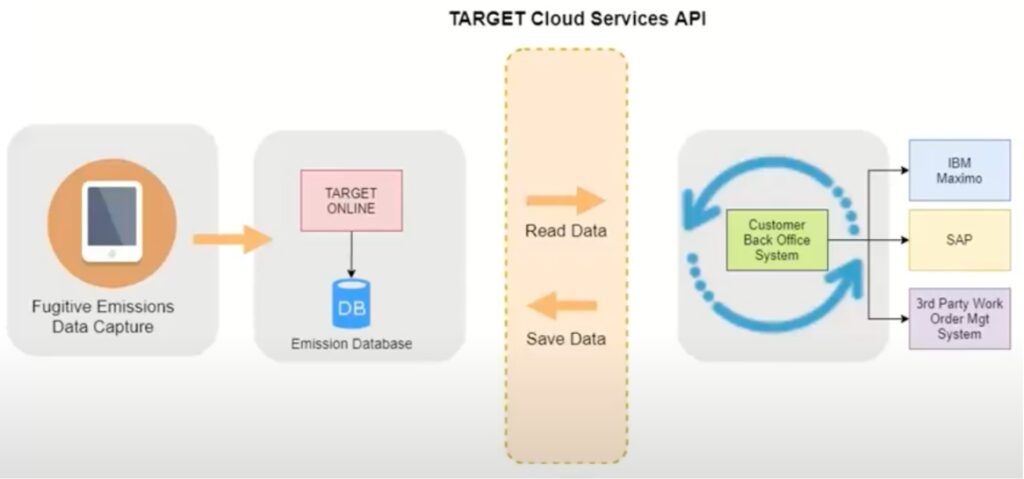
Why optimizing your OGI surveys is a better alternative to Method 21
Is AWP worth the effort to overcome these OGI pitfalls? In short, the answer is undoubtedly yes. Anything worth doing is worth doing well—and investing in proper OGI training and overall LDAR data management will deliver huge returns in no time flat. To prove it, let’s dispel some of the biggest myths regarding OGI cameras and Method 21 detection devices.