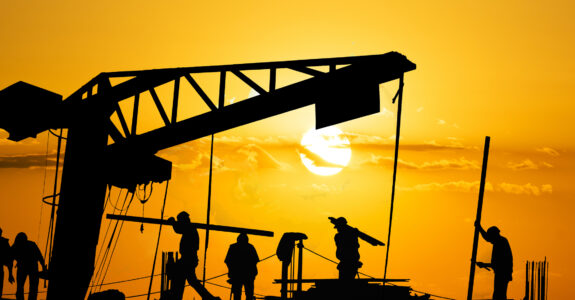
Heat Safety in the Workplace: A Look at OSHA’s Proposed New Rule
August 9, 2024
By: Michael Morrison
On July 22nd, 2024, the world experienced its hottest day on record since such measurements began, according to a NASA analysis of global daily temperature data. Throughout this summer, major US cities such as Tampa, San Francisco, Phoenix, Las Vegas, Boston, and many others have broken records for daily high temperatures. Extreme temperatures cause hazardous work conditions due to the dangers of heat and heat-related illnesses. Heat is also the leading cause of death among all hazardous weather conditions in the US. To address this issue, on July 2nd, OSHA released a proposed rule with the goal of protecting workers from the significant health risks of extreme heat.
Heat Injury and Illness Prevention in Indoor and Outdoor Work Settings
If the proposed rule is approved, it will apply to all employers and will be triggered when employees are exposed to heat indexes of 80 degrees F or above for more than fifteen minutes in any sixty-minute period. If triggered, the rule would require employers to:
- Conduct Regular Heat Risk Assessments – Evaluation of the potential for heat exposure in various job roles and settings (including indoor and outdoor work).
- Monitor Workplace Temperatures – Implementation of systems to continuously monitor temperature and humidity levels.
- Preventative Measures:
- Hydration – Provide workers with accessible drinking water at all times
- Rest Breaks – Implementation of scheduled rest breaks in cool or shaded areas. The frequency and duration of these breaks will need to increase with rising temperatures.
- Shade and Cooling areas – Ensure that shaded or air-conditioned rest area are available for workers to use during breaks.
- Training and Education:
- Provide Heat Safety Training – Education on the dangers of heat-related illnesses, the symptoms, and the importance of preventative measures. Conducted on an annual basis.
- Acclimatization Programs – Develop and implement acclimatization plans for new and returning workers.
- Emergency Planning and Response:
- Employers with more than 10 employees will be required to develop and implement a Heat Injury and Illness Prevention Plan (HIIPP).
- Emergency Medical Response – Develop a heat emergency response plan and ensure that supervisors and workers are trained on the plan.
- Recordkeeping and Reporting:
- Maintain Indoor Monitoring data for a minimum of six months.
- Maintain records of heat-related incidents, including illnesses and near-misses.
- Conduct regular audits of heat safety measures and compliance with the standard.
- Additional Requirements for High-Risk Industries (specific industries such as agriculture and construction)
- Enhanced protections such as more frequent rest breaks, specialized training, and more rigorous monitoring of conditions.
- Enhanced protections for vulnerable populations
The expectation is that this rule will become final in the first half of 2025. However, there are two substantial dynamics that may factor in the finalization of the rule. The first is a possible change in executive leadership in the White House in January 2025, which could derail the current proposed rule. Second, due to recent SCOTUS rulings (i.e., the overturn of Chevron), there could be court proceedings and challenges to the rule that delay the rule from taking effect or block it entirely.
Prepare for Heat-Related Inspections
In addition to the rule proposal, OSHA continues to conduct heat-related inspections under its National Emphasis Program. Since the launch of the program in 2022, OSHA has conducted nearly 5,000 heat-related inspections. OSHA encourages employers to download and use the OSHA Heat Safety Tool application for iPhones and androids, as the app allows employers to calculate the heat index for their worksite and based on the index, display a risk level to outdoor workers. Also in the app are reminders of protective measures based on the risk level.
States Take Early Action on Heat Safety
Some states have decided to take action prior to the proposed OSHA rule due to increasing temperatures seen across the country. As of October 2021, four states have promulgated hazardous heat standards requiring employers in various industries and workplace settings to provide protections and abatement measures to reduce the risk of heat-related illness for their employees: California, Minnesota, Oregon, and Washington. Oregon issued a temporary rule in July of 2021 after experiencing temperatures well above 100 °F for an extended period. Washington State also issued emergency heat rules during the summer of 2021 that provide additional worker protections to its previously promulgated heat rule. Additionally, since 2020, three more states, Colorado, Maryland, and Nevada, have passed laws requiring state health and safety administrators to promulgate rules related to hazardous heat in the workplace. Virginia’s Safety and Health Codes Board is also considering a standard on this topic. These state-level initiatives highlight the growing recognition of the need for comprehensive regulations to protect workers from the dangers of excessive heat.
As temperatures continue to rise and extreme heat events become more frequent, it’s crucial for employers to put the safety and well-being of their workforce first. Montrose’s Environmental, Health and Safety & Security (EHSS) professionals are well-positioned to assist in the development of a Heat Injury and Illness Prevention Plan (HIIPP), Heat Emergency Response Plan, and training and education material. Our EHSS team’s extensive auditing experience can also provide a regulatory gap assessment of your program against OSHA’S proposed Heat Rule so that you are ready if it becomes law. By implementing these effective measures now, you can prioritize your employee’s health and wellness and stay ahead of future regulations.
Contact us now to safeguard against heat-related injuries and illness.
Sources:
- Heat Safety Tool | Occupational Safety and Health Administration (osha.gov)
- Heat Injury and Illness Prevention in Outdoor and Indoor Work Settings Rulemaking
- Department of Labor takes critical step in heat safety rulemaking
- Biden-Harris administration announces proposed rule to protect indoor, outdoor workers from extreme heat
- Update: Proposed OSHA Heat Rule Available Now
- OSHA Releases First-Ever National Heat Safety Rule
- OSHA’s Proposed Heat Injury and Illness Prevention Standard in Focus
- NASA Data Shows July 22 Was Earth’s Hottest Day on Record
- Here Are The U.S. Cities Breaking Heat Records This Summer
Michael Morrison
EHS Consultant II
Mr. Morrisson is an experienced EHS professional with several years of auditing experience in various industries while working at Montrose, including railroad, oil and gas, food and beverage manufacturing, and several PSM-covered facilities. Mr. Morrisson has served as lead auditor for over 50 audits, demonstrating a strong expertise in regulatory compliance, resulting in improved environmental practices and compliance strategies for audited clients. Mr. Morrisson also has experience building EHS programs for these companies, ranging from general compliance programs to certification programs such as ISO 14001. Prior to his time at Montrose, Mr. Morrisson worked in the private sector, both managing and auditing various environmental programs including Air, Stormwater, Hazardous waste, PWS, EPCRA, and Wastewater.