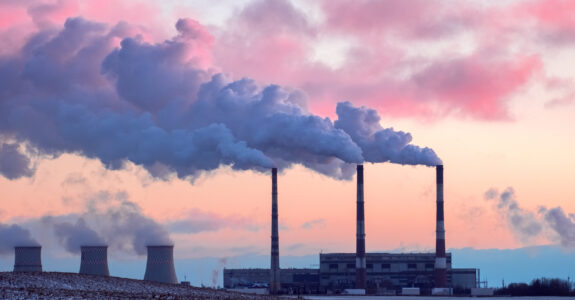
Best Practices for Semiconductor Stack Testing
April 5, 2024
By: Blake Ericson
In the world of semiconductor stack testing, no one can afford to cut corners when monitoring emissions and compiling data. Emissions testing within the semiconductor space is a relatively new practice and anticipated to not only grow, but become more stringent with time. If you’re relying on a firm without a proven track record or opting for inferior technology because of a relatively low price point, then cutting corners is exactly what you can expect. And like every shortcut, there are potential tradeoffs. In this case, you’re likely harming the reliability of your data, compromising your analyses, and worst of all, potentially prolonging the exposure of your on-site teams to dangerous air quality conditions.
Fortunately, there are best practices you can adopt to eliminate these shortcuts. Once you do, you can remove blindspots and errors from your data, improve the accuracy of your data interpretations, and optimize systems. The result will be increased overall stack testing efficiency (which leads to lower costs) and a greater ability to achieve and maintain regulatory compliance. Since the EPA plans to continue its review and expansion of Method 1, Method 2, and Method 320 requirements, specifically in the semiconductor space, implementing these best practices now will undoubtedly set up your stack testing programs for success in the future.
Monitor stack emissions with FTIR technology
Fourier transform infrared spectroscopy (FTIR) technology enables real-time monitoring of stack emissions. It analyzes and shares valuable information based on how specific compounds interact with infrared light. This is a particularly effective technology for stack testing in semiconductor manufacturing, which involves the etching of silicon wafers and the cleaning of chemical vapor deposition chambers. FTIR can see a comprehensive list of analytes of interest in the semiconductor space from the typical processes found in operations. These processes either use or produce:
- Various perfluorocarbons and hydrofluorocarbons
- Nitrogen trifluoride
- Sulfur hexafluoride
- Combustion byproducts
Facility operators use abatement technologies throughout their semiconductor facilities to combat the emissions produced by the tools used in the manufacturing of silicon wafers. These technologies include point of use (POU) abatement systems to reduce or eliminate the release of the gases listed above. FTIR technology enables real-time, on-site measuring of how effective these systems are at controlling emissions by determining the destruction rate efficiencies (DREs) of each POU system. In short, FTIR technology is invaluable for both compliance and engineering purposes.
Conduct FTIR data validation
FTIR data validation is important because it confirms whether or not concentrate data is accurate. Validation is a requirement within the USEPA Methodology and is often overlooked. It is a critical component of all parts of testing via FTIR and ensures you and your firm are satisfied with the data quality and allows for the facility to make sound decisions in a timely manner. FTIR data validation consists of three sections:
FTIR diagnostics
Running diagnostics on FTIR technology confirms that the FTIR will generate useable spectra and that the type of FTIR is the best fit for the test objective.
Data analysis
This involves manually comparing reference spectra to sample spectra and manual concentration results to software-generated results. Conducting data analysis allows operators to optimize the FTIR technology’s quantitative method based on the manual analysis by adding and removing compounds and reprocessing data if necessary.
QAQC processes
A stack testing firm should have the QAQC processes in place to validate data and ensure a high level of data quality and confidence. QAQC must-haves include:
- Knowing the ins and outs of your chosen method
- Conducting direct calibrations
- Performing system checks
- Spiking
- Ensuring proper cylinders are being used within acceptable concentration ranges
- Maintaining clean delivery to your instrumentation
Work with qualified operators, chemists, and other experts
The team in the field is just as critical as the technology used for semiconductor stack testing. You need operators who understand how FTIR technology works and how to best capture emissions data. Likewise, you need seasoned experts who understand how to handle and interpret that data. FTIR technology is only part of the quality equation. It takes a well-qualified team to:
- Test and calibrate FTIR components
- Ensure FTIR equipment is generating data correctly
- Collect emissions data in the most efficient—and safest—way possible
- Interpret data with a high degree of accuracy
- Meet the strict reporting requirements within the semiconductor space
Benefits of FTIR for monitoring stack emission levels
Montrose has partnered with semiconductor facility operators to conduct semiconductor stack testing with great success. Specifically, when testing for greenhouse gases (GHG) on POU systems, not all systems individually meet the DRE requirements and need to be optimized. Facilities have the ability to calculate emissions based on theory and expected values, but what is often found is that emissions and DREs are different than what is anticipated and promised by the vendors.
When best practices like the ones outlined above are followed, these facility operators are seeing tangible benefits such as:
Cost savings
The real-time monitoring of FTIR technology allows users to optimize abatement equipment on site with less mobilizations. Systems can also be optimized on site without the need for shipping costs.
Time savings
Instead of having to send samples to a lab, which usually come with turnaround times of three to four weeks, FTIR technology enables emission testing to be conducted within two to four hours after our team’s arrival.
Regulatory compliance
Essentially, FTIR takes “photographs” of spectra and saves them for data validation. This information is critical to ensuring the high-quality, precise measurements because it is an extra step not typically found in other traditional stack testing methods. FTIR has the capability of seeing several compounds simultaneously, thus allowing facilities to achieve their compliance goals without the need for several test methods.
Achieve greater stack testing efficiency and safety at your semiconductor facility
We can review your existing testing program, even if it already utilizes FTIR, to find opportunities for procedural and technological improvement. We can also assist with CEMS installation, develop, and deploy an active FTIR sampling strategy, and work to make sure you have highly effective and efficient semiconductor stack monitoring and testing capabilities. Get in touch
Blake Ericson
National Business Development Manager
Blake Ericson has almost a decade of experience in the fields of air quality management, engineering, and regulatory testing – primarily with Fourier transform infrared (FTIR) technologies. He is focused on promoting and expanding understanding of how these complex technologies can assist all stakeholders involved with air quality management. Blake has managed hundreds of successful projects, domestically and internationally, for industrial sectors including power generation, chemical manufacturing, pharmaceuticals, and cement. He has also supported development of tests, methods, and technologies currently in use for source testing. Blake holds a BS in Chemistry and an MBA from Central Michigan University.